Jul 10, 2025
We Still Need to Mine. So, Let's Think About it Differently
Changing our perceptions around mining for our material future.
July 10, 2025
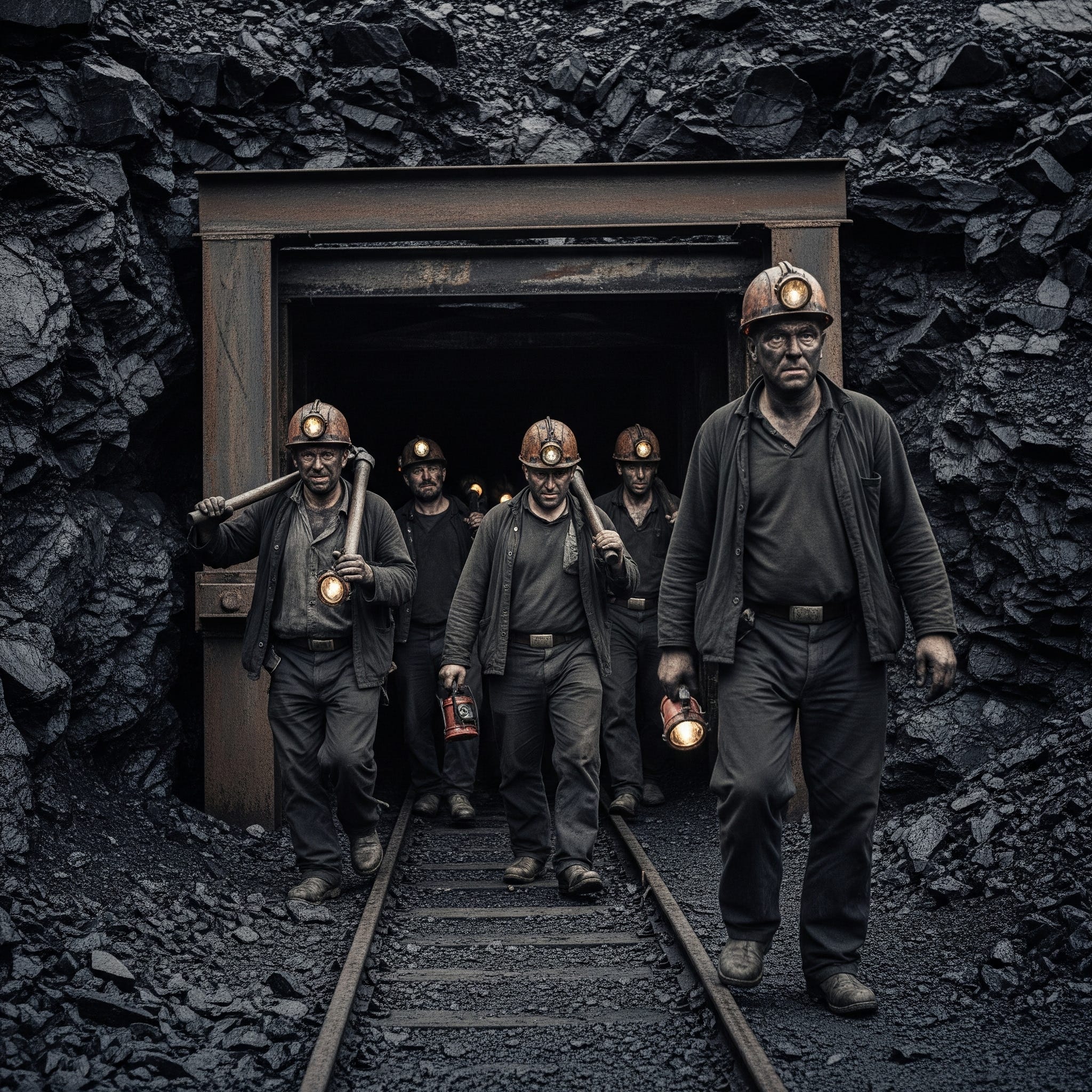
What I remember most is my father’s respirator.
Every working day between the ages of 19 and 54, my father descended 600 feet below the rolling Appalachian foothills of Western Pennsylvania into a bituminous coal seam. Unlike the generations of miners before him, my father wore a respirator with a replaceable filter. When he returned home from his rotating shifts, he would place his lunch bucket, water jug, and respirator on the kitchen counter. The previously white filter was as black as you can imagine catching at least some of the toxic coal dust that caused black lung before my father breathed it in. Working for decades in dark and dangerous conditions and having seen friends die, my father gave me two directives I knew better than to ever question or break:
Frontier Foundry Substack is a reader-supported publication. To receive new posts and support my work, consider becoming a free or paid subscriber.
Never go into the mine.
Never cross a picket line.
For centuries, miners have been giving these directives to their sons. The cycles have repeated with black faces and black lungs emerging from mines generation after generation. However, the reality of mining in the decades to come is not as black and white as my father’s respirator. We cannot escape mining. If we want to manufacture goods, we need raw materials. To get raw materials, we need to take them out of the Earth. The raw materials we need are rare earth elements (REE) and critical minerals , and we need to mine them.
I am as well positioned as anyone that never worked in a mine to understand the negative perceptions around mining. The coal seam my father mined used a longwall shearer , a particularly controversial method of mining consistently blamed for cracked foundations and sinking homes. Decades later and with significant advances in technology and the global imperative, mining is different. We can think beyond drilling new shafts, blowing the tops off mountains, and company stores. Mining has been a dirty and exploitative business for all human history, I witnessed it. But mining is no less essential.
The U.S. and its allies must begin building a mining industry that makes economic and environmental sense and is sustainable for decades, and centuries, to come. But a change in perception is in order. Future innovations will depend on the right raw materials to create critical components such as industrial magnets . The technology is only part of the story.
Changing how we view mining is step one. We also need to change the economic model around mining, the subject of a future post. Let’s start at the surface.
Subscribe now
What was Old is New Again The history of mining is about productivity. Productivity in mining means how much rock an individual miner can extract from a mine per year. Here’s a brief timeline:
Pre-1892
Manual labor using hammers, chisels, picks, shovels, and fire.
Productivity: ~.5 tons per miner per year.
1892-1946
Introduction of black powder to break large rock faces into small pieces. Still required manual labor.
1946-1995
Mechanical drills powered by steam and electric mine cars.
Productivity: 4,000 tons per miner per year.
The average productivity per miner has not shifted significantly since modern mining techniques were introduced in 1995 to include hydraulics. That’s just on the methods. There’s more.
Digging mine shafts has also gotten more challenging over time as geological surveying processes have improved and mines have been required to go deeper. Due to transport requirements for the mined material, shafts must be dug at a certain gradient so the loaded vehicles can climb out of a mine that may be over a mile deep. This requires additional digging and drilling at a significant time and financial investment. A fresh mine shaft may not be operational for over a decade before it can start producing materials, let alone turning a profit. Environmental impacts are also a serious concern with the creation of new mine shafts.
The question here should be obvious: Why dig new mine shafts?
Exactly.
According to the Centers for Disease Control (CDC), there were 12,616 active mines in the US in 2023 across multiple sectors. The Office of Surface Mining Reclamation and Enforcement in the US Department of the Interior has data on over 274,000 abandoned surface and underground mines in the US. That means there are at least 286,616 mine shafts already dug in the US alone. With that number of shafts already available, we should not be thinking about drilling new ones but should instead be thinking about how to get out of them what we need in a more economical and environmentally sustainable way.
Image Credit
Abandoned mines are abandoned for a reason, right? Yes, but there’s an important distinction.
Thousands of mines were likely abandoned at a time before we knew to look for things like REEs or other critical materials that are important to our society today. No one was looking for yttrium before products and processes were invented that use yttrium.
There are also mines that were abandoned due to economics or financial mismanagement. That does not mean they are necessarily “dry” but that they closed for outside reasons. There are comments to be made about the irresponsibility of drilling mine shafts without the economics to make the sacrifice worth it, but that’s outside this scope. What’s within our scope is that we don’t have to make this mistake again.
The technology is available to survey those existing mines for the presence of REEs or other critical minerals and a huge portion of the overhead of project will be reduced by avoiding the 10–20-year process of drilling new mine shafts. And now that we know what we are looking for, we can be smarter about how we allocate our resources. As discussed in a previous post, the “proved reserves ” number only refers to reserves of REEs we know about. If we haven’t looked, there may be more REEs available domestically than we realize. If this sounds unrealistic, recall that an underground reservoir of lithium brine so large that it is estimated to contain 9 times the global lithium demand for car batteries in 2030 was just discovered in October 2024, less than a year ago as of this writing. It’s in the Smackover Formation and it is worth looking up.
Image Credit
Share
Underground “You can be anything you want to be. Just never go into the coal mine.”
As a child this frequent warning from my father made little sense. Coal miners had cool helmets with lights on the front, which made for a pretty fun costume, so what was the problem? It wasn’t long before I understood it completely. Working underground on rotating shifts might feed your family, but it was a hard existence. While Americans might feel nostalgia for the availability of industrial jobs like these, many miners would just as soon prefer never to go back underground. One can hardly blame them.
Another obvious question: Why continue sending humans underground?
Exactly.
The technology exists today to run and manage autonomous mining equipment underground that requires no humans to spend considerable time underground with the possible exceptions of inspections and maintenance. Human controllers can work above ground in air-conditioned rooms with windows and extract considerably more rock than multiple individual miners combined. This is not only more economical and less exploitative, but also more productive. The economics of mining change entirely if you are no longer drilling new shafts, not putting humans underground, and removing much more rock.
Using autonomous robotic mining, existing mine shafts can be used to extract upward of 20,000 tons of rock per person per day . The volume of rock extracted with lower overhead completely changes the economics of mining and removes the requirement to continue defacing our planet with more strip mines. Fewer black faces and lungs, more of the materials we need.
At least my father had a respirator.
He also had trains to move the rock out of the mine and longwall shearers to remove it from the coal seam. Much better than picks and pushing carts by hand by any measurement. The old timers that my father remembers when he was brand new had no such relative luxuries. The men those old timers called old timers had even less. This is the human side of technological progress.
The problem with mining is its arc of that technological progress has been defined by human and environmental exploitation. That is the narrative, and it is well documented. Small wonder that people don’t want more mines drilled or more sons or daughters going into them to mine rock.
But here’s the other thing about technological progress; it changes narratives.
We can’t escape mining.
Building and manufacturing require raw materials from fuel to REEs to critical minerals. Emerging technologies will require new materials, and those new materials will require creative ways to combine raw materials to build what we need. But mining does not need to be like it was for my father or for the old timers before him. Autonomous mining equipment in existing shafts that are scanned for the specific materials we are looking for is not a dream scenario. It may sit beyond what my father thought was possible, but the technology exists today, and its implementation has real impacts for the world.
The world needs access to mined material and mining on the moon, an asteroid, or deep in the ocean is considerably more difficult and more expensive than doing it in existing mines on land. Our need and ambition should not blind us from the obvious answer. REEs are a vital part of our material future. Let’s dust off our faces and think about how we can do this sustainably and without the historical exploitation that we see in the dirty faces of miners past. That I saw in my father’s respirator and that he saw in the faces of the old timers.
I never have gone into a mine, and I still won’t cross a picket line. Maybe no one else needs to.
Leave a comment
Nick Reese is the cofounder and COO of Frontier Foundry and an adjunct professor of emerging technology at NYU. He is a veteran and a former US government policymaker on cyber and technology issues. Visit his LinkedIn here .
Frontier Foundry Substack is a reader-supported publication. To receive new posts and support my work, consider becoming a free or paid subscriber.